RESEARCH
The research group aims at understanding the deformation and fracture of materials on the nano- and microscales. Our approaches are based on not only fundamental solid mechanics but also nano- and micromechanics considering dislocations, grain boundaries, interfaces and surfaces. We develop experimental methods for evaluating mechanical properties and strength of nano- and micromaterials such as thin films, nanowires, and nanotubes. Our techniques include fabrication of nanostructures by self-assembly, specimen preparation by lithography and focused ion beam, nanomechanical testing using nanoindentation and nanoscratching technologies, and observation of deformation and fracture by atomic force microscopy and electron microscopy. Applications of our study include nano- and micro electromechanical systems (NEMS/MEMS), microelectronic devises, and nanotechnological devices.
Nanomaterials
Phenomena of interest include deformation and crack propagation behavior in freestanding nano-films, deformation and fracture of nanocolumns, nanosprings, and nanotubes, crack initiation and propagation at their interfaces, mechanical and physical properties of nanostructured surfaces. Since the strength and fracture of materials depend on loading and environment, we develop experimental methods under not only monotonic loading but also cyclic loading (fatigue), elevated temperature (creep), and corrosive environments.
Recent highlights
Mechanical properties and strength of freestanding nano-films
To clarify the size effects in plasticity and fracture toughness of metallic nano-films, we develop tensile and fracture toughness experiments for freestanding films. In copper films with 100 nm ~ 500 nm thicknesses, crack propagates stably before unstable fracture. A clear size effect is observed where thinner films have smaller toughness. Fracture morphology transits from ductile to brittle with decreasing film thickness.
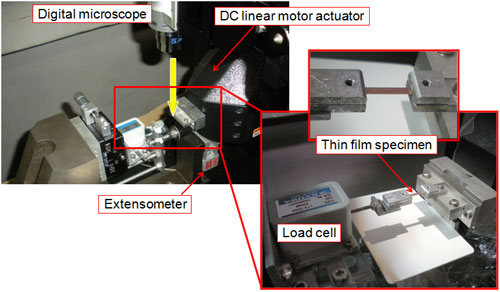
Tensile experiment for freestanding nano-films
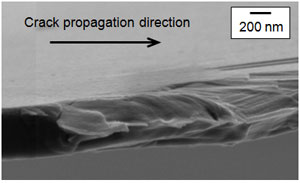
Fracture surface of a Cu film
References
"Size effect on fracture toughness of freestanding copper nano-films"
Materials Science and Engineering A, Vol. 528 (2011), pp. 8120-8127.
Fatigue and creep properties of freestanding nano-films
We develop experimental methods for exploring fatigue and creep properties of nano-films. Our experiments reveal, for example, submicron-thick aluminum films show typical creep behavior consisted of transient, steady state, and accelerated creep regions. We study the fundamental mechanisms and dominant mechanics of subcritical crack growth due to fatigue and creep and their size effects.
![]() Creep experiment for freestanding nano-films |
![]() Creep behavior of an Al nano-film |
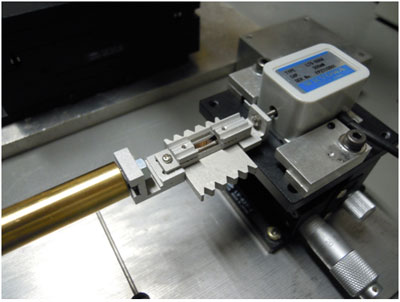
Fatigue experiment for freestanding nano-films
References
"Thickness effect on steady state creep properties of freestanding
aluminum nano-films"
Acta Materialia, Vol. 60 (2012), pp. 4438-4447
Related topics (references)
“Hydrogen Effect on Fracture Toughness of Thin Film/Substrate Interfaces”
Engineering Fracture Mechanics, Vol. 77 (2010), pp. 803-818
Self-assembly
Self-assembly or self-organization can realize structured or sculptured nano-elements. For example, glancing angle deposition (GLAD), wherein the incident angle of vapor deposition is highly inclined to the substrate normal, enables the fabrication of discretely-grown oblique nanocolumns. By controlling the rotational angle of the substrate during the deposition, structured nano-elements with helicoid, zigzag, pillar, and other shapes can be formed. Because of the great variety of possible shapes, the structured nano-elements have the potential to be mechanical elements in novel nano- or micro-electromechanical systems.
Our research group develops fabrication concept of novel nanostructures using self-assembly, and studies the mechanical properties of the nano-elements by original methodology.
Recent highlights
Interface strength of nanocolumns grown by glancing angle deposition
We develop a loading method for nanocolum arrays using a micro-brick specimen, and conduct interface fracture experiments on oblique Ti nanocolumns grown on a Si substrate by GLAD. The results reveal clear anisotropy in the interface strength due to an asymmetric nanostructure. Our results indicate the possibility that GLAD can realize micro- and nanoscale devices with arbitrary strength and its anisotropy by controlling the shape of the constituent nano-elements.
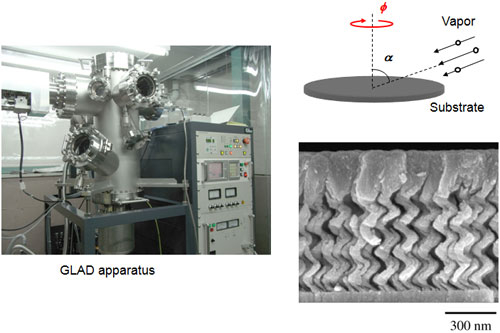
Nanospring array grown by glancing angle deposition
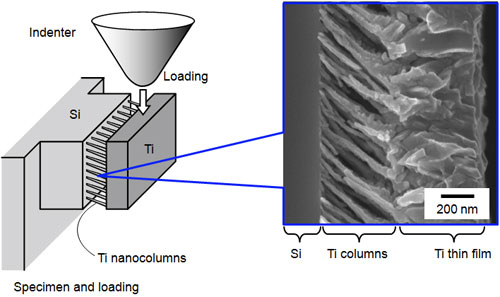
Mechanical loading experiment for nanocolumn arrays
References
"Interface strength of structured nanocolumns grown by glancing angle deposition"
Engineering Fracture Mechanics, Vol.78 (2011), pp. 2800-2808.
Fabrication of freestanding flexible nano-films by mechanical self-assembly
We propose a technique for producing freestanding nano-films having a wrinkled structure using mechanical self-assembly. In an experiment, we discovered that a wrinkle pattern can be made on the surface of a sacrificial resin layer by applying compressive strain under the appropriate conditions. Using this phenomenon, we made a freestanding wrinkled film by depositing a film on the wrinkled resin surface and then removing the resin layer with an organic solvent. Uniaxial tensile tests for 300-nm-thick freestanding copper wrinkled films revealed that the films have superior deformability: the fracture elongation is more than 10 times larger than that of its straight film counterpart.
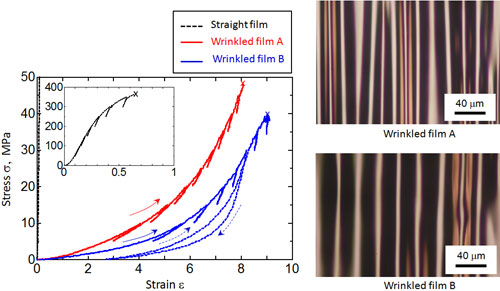
Tensile experiments of wrinkled Cu films
References
“Realization of Freestanding Wrinkled Thin Films with Flexible Deformability”
Applied Physics Letters, Vol.98 (2011), pp. 041908-1-3
Related topics (references)
“Strength of Self-Organized TiO2 Nanotube Arrays”
Acta Materialia, Vol. 58 (2010), pp. 4956-4967
"Frictional anisotropy of oblique nanocolumn arrays grown by glancing angle deposition"
Tribology Letters, Vol.44 (2011), pp. 259-268.
"Fabrication and Mechanical Properties of Column-Particle Nanocomposites by Multiscale Shape-Assisted Self-Assembly"
Journal of Physics D: Applied Physics, Vol. 45 (2012), 025302.
Indentation mechanics
Among various mechanical testing methods, indentation is a particularly convenient way to probe mechanical property such as elastoplastic property and fracture characterization of materials, since the method involves very little effort on sample preparation. We are challenging to develop novel techniques to evaluate mechanical property on the basis of indentation mechanics. Recent projects have addressed elastoplastic property evaluation and contact fracture characterization using both computational and experimental approaches. The projects further extend to address
1) Evaluation of local and anisotropic plastic property
2) Susceptible evaluation for hydrogen embrittlement and hydrogen absorption technique
3) Formation of self-assembled crack patterns
4) Global environmental and energy challenges
Some projects have been collaborated with other institutes and supported by industrial community. For more information, please contact us.
Recent highlights
Evaluation of susceptibility to hydrogen embrittlement cracking using indentation test
Toward development of hydrogen energy system, high strength steel with hydrogen absorption may suffer strength degradation, namely hydrogen embrittlement cracking (HEC) usually occur. This is still important issue, and the strength evaluation is required for their intended use. We have focused on indentation cracking in the high strength steel with hydrogen absorption. Hydrogen content in the material is evaluated by thermal desorption spectroscopy system. The mechanism of indentation induced hydrogen cracking is investigated by finite element method. These insights provide noble approach for evaluating critical strength for hydrogen environment.
![]() Hydrogen embrittlement cracking in high strength steel by indentation |
![]() Crack growth analysis of indentation process |
References
“On Hydrogen-induced Vickers Indentation Cracking in High-strength Steel", Mechanics Research Communications, Vol.37, pp.230–234 (2010)
“Evaluation of Susceptibility to Hydrogen Embrittlement Cracking in High Strength Steel using Indentation Test”, 2009 ASME International Mechanical Engineering Congress & Exposition
Related topics (references)
Incipient plasticity of gold nano-films
“Evaluation of Incipient Plasticity from Interfaces between Ultra-Thin Gold Films and Compliant Substrates”, Thin Solid Films, Vol. 518 (2010), pp. 5249-5256
Evaluation of anisotropic plasticity by indentation
“A Simple Method to Evaluate Anisotropic Plastic Properties Based on Dimensionless Function of Single Spherical Indentation - Application to SiC Whisker Reinforced Aluminum Alloy –”, Materials Science and Engineering A,Vol.527, pp.7646–7657 (2010)
Experimental equipments
![]() Apparatus for fatigue experiment of nano-films |
![]() Apparatus for creep experiment of nano-films |
![]() Handling apparatus of freestanding nano-films |
![]() Nanoindenter (Agilent Nanoindenter SA2) |
![]() Nanomechanical testing system (Hysitron Triboscope) |
![]() Micro-force testing system (MTS Tytron 250) |
![]() Atomic force microscope (Veeco Dimension 3100) |
![]() Glancing angle deposition machine (Eiko Engineering) |
![]() Scanning electron microscope (JEOL JSM-5300S) |
![]() Electronic discharge machine (Mitsubishi Electric PX05) |
![]() Thermal desorption spectroscopy system (ULVAC TDS-KU) |
![]() Micro compression testing machine (Shimadzu MCTM-500) |
![]() Hydraulic servo fatigue testing machines (Shimadzu Servopulser) |
![]() Hydraulic servo fatigue testing machines (Shimadzu Servopulser) |
![]() Field Emission-Scanning Electron Microscope (JEOL JSM-7001F) |
![]() Electron Backscatter Diffraction Analysis System (TSL OIM, EDAX OIM Analysis System) |
![]() Stylus-based surface profiler (Tencor ALPHASTEP) |